On the basis of the original magnetic polishing machine, the translational magnetic polishing machine adds 2-3 units of magnetic field to move left and right, which greatly improves the uniformity of the entire polishing. The product has no blind spots in the grinding barrel, especially in the center and surrounding positions of the disk.
Advantages of translational magnetic polishing:
1.Because there is no central and surrounding blind spots for polishing small parts, the processing weight can be greatly increased, and the polished products are uniform and more efficient.
2.The uniformity of polishing large parts is high, including brightness and sand surface, and the uniformity of deburring is extremely high. (The reason is that large parts are too large to roll freely)
3.On the basis of the original circular shape, the translational polishing machine greatly increases the length of the magnetic field area because it moves back and forth left and right, which is suitable for polishing longer products.
Translational magnetic polishing machines are more suitable for large quantities of parts such as large, long tubes and deep holes of complex parts, deburring and polishing of holes in cavities, and have high requirements for the quality of the processing surface and the inside of the hole. The parts that cannot be processed by manual and traditional methods can achieve large-scale processing without damaging the workpiece, improve efficiency and quality, and machine grinding has no dead angles.
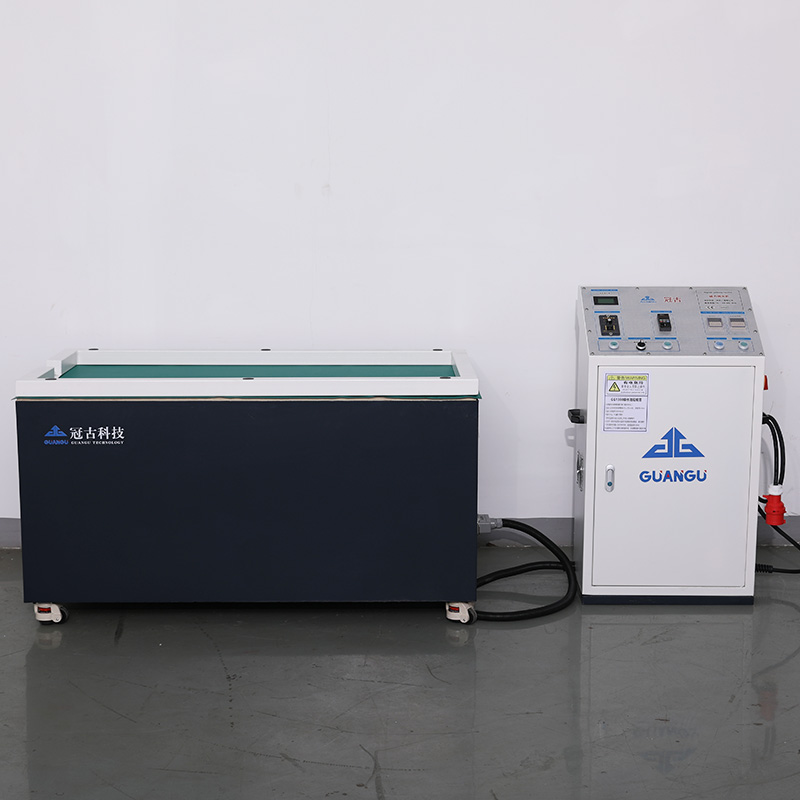
Working principle
Magnetic polishing/grinding/Indiadeburring machine uses the power of high-strength magnetic field to guide the stainless steel magnetic needle to produce rapid rotation to grind the workpiece, so as to achieve efficient removal of burrs, burrs, polishing, polishing, descaling, welding spot removal and other grinding effects on the surface of the product.
Equipment advantages
Magnetic polishing/Indiagrinding machine can perform all-round non-dead angle grinding on metal workpieces, including precision grinding of irregular parts such as inner holes, crevices, right angles, threads, etc. The equipment has stable performance, high efficiency and high speed, and the average grinding time is about 3-20 minutes.
For irregular shaped parts, burr removal, polishing, Indiacleaning and grinding are completed at the same time.
Fast grinding speed, one-button operation, simple and safe, one person can operate multiple machines, low consumables use cost, high grinding efficiency.
After grinding, the product will never be deformed, the surface will never be damaged, and the accuracy will never be affected.